|
|
How To And Tips
|
 |
10 Summer Construction Safety Tips — For You and Your Equipment
Summer’s a busy season for construction sites with no time for downtime. These safety tips will help keep your team and equipment healthy, safe and on the job.
By Lonnie Fritz, Senior Market Professional – Construction Industries, Caterpillar Inc.
There’s a lot to love about summer: warm temps, plenty of sunshine, long days and your choice of outdoor activities. But on the jobsite, summer’s advantages can quickly turn into disadvantages. Heat-related illness is real, common and can lead to severe complications or even death. Hotter temperatures also cause machines to work harder, stressing components and accelerating wear. How can you keep your people and your fleet safe this summer? Start here:
5 ways to protect your team (and yourself)
- Eat and drink right. Don’t skip meals or overeat. Your best bet is to eat lighter (no heavy, greasy foods) during the hottest part of the day and aim for eight ounces of cool water every hour.
- Dress properly. Wear lightweight, light-colored, moisture-wicking clothes — and don’t forget to put on sunscreen and sunglasses.
- Pay attention to your body. If you feel dizzy or lightheaded, tell someone and find a cool, shady spot to rest. Refrain from going in and out of the air-conditioning, which puts more strain on the body. If possible, adjust working hours to the coolest part of the day or to nighttime hours.
- Know the signs. Heat exhaustion (fatigue, disorientation, nausea, headache, rapid heart rate and clammy skin) can quickly escalate to heat stroke (elevated body temperature, loss of consciousness, convulsions, vomiting and diarrhea). Learn to recognize the signs in yourself and others.
- Keep an eye on your coworkers. Victims of heat exhaustion or stroke aren’t always aware of what’s happening, so if you see someone struggling, alert a supervisor and call 911 if necessary. Pay special attention to those who are 65 and older, overweight or on medication.
5 ways to protect your machines
- Beef up inspections. Check hydraulic fluid level, engine oil level, coolant level, radiator cap seal and pressure, hoses, air conditioning, tires and tire pressure every day. Use fluids and lubricants designed for your climate conditions.
- Clean it up. Remove debris from radiators, cooling systems and engine hood inlets and outlets daily.
- Talk technique. Encourage operators to shift smoothly, accelerate steadily, turn gradually, travel at controlled speeds and avoid spinning the wheels.
- Track temperatures and pressures. Telematics data can be a big help in monitoring equipment status, predicting potential problems and planning repairs before failure.
- Shutdown and store machines correctly. Follow the manufacturers machine shutdown procedures to ensure the machine cools down before shutting off. Where possible, keep any machines not in use out of the sun in a dry, sheltered area.
During the summertime as we battle the heat and humidity, it’s also a good time to review personal hygiene practices on the jobsite and in the office. So in addition to the above, remember to wash your hands, keep common areas and machines sanitized and stay home if you’re sick. Summer’s a busy season for construction sites with no time for downtime. These safety tips will help keep your team and equipment healthy, safe and on the job.
5 Tips to Safely Purchase, Handle and Store Diesel Exhaust Fluid This Summer
Five tips to help you safely purchase high-quality, API-certified DEF and to handle and store it in a way that protects it during the warm weather months.
June 15, 2020
By Jeffrey Harmening - Equipment Today
DEF is made from a mixture of technically pure urea and purified water and must be handled and stored properly to preserve its quality. Handling and storing DEF in warm weather requires special care to protect it from the impact of high temperatures, which can decrease its useful life. Now with the need for added safety in public places, dispensing DEF at service stations will require extra care.
To ensure that equipment operators and people working in shops are safe, the American Petroleum Institute (API) has developed several tips for equipment operators and for shop owners to help them purchase high-quality DEF in a safe manner and to handle and store it so as to protect it during warm weather months.
1. Purchasing DEF at a Service Station
On the road, one of the main challenges is knowing the actual brand of DEF being sold. While regulations in many states require identifying the manufacturer and brand on receipts, some locations do not include it. API recommends purchasing DEF that is clearly identified at the fill-up location.
In addition, those accustomed to purchasing DEF in containers should look at the expiration date if it’s printed on the bottle and be sure to use it before this date as the product has a limited shelf life. If an expiration date is not present, look at the traceability code for a date. This date is usually equivalent to the packaging date. As a last resort, ask for the most recently delivered DEF products. Storage conditions also have an impact on its quality. DEF can be expected to have a minimum shelf life of 12 months or even longer in optimum conditions.
2. Safely Dispensing DEF
As many gas station and truck stop owners around the country have taken steps to increase the cleaning frequency of the high-touch points, there are recommended practices to help everyone protect themselves at the pump. Consider the following when dispensing DEF or fuel:
- Follow the CDC’s recommendations to clean your hands often, practice social distancing and wear face coverings.
- Consider using gloves or paper towels while touching surfaces.
- Carry hand sanitizer or sanitizing wipes with you and use them both before and after fueling.
3. DEF Storage in a Vehicle
Check the label on the bottle for recommended storage temperatures and be sure to look for the API certification mark as well. API recommends that you don’t store DEF for too long in a vehicle, especially if the storage area in the vehicle is routinely hotter than the recommended storage temperatures displayed on the label.
DEF stored at 86° F and above will only last about six months. Exposure to direct sunlight may also decrease the life DEF.
4. Purchasing DEF for Shop Use
API has found that the biggest misconception by fleet managers is the belief that if the urea concentration of their DEF is on spec, then the DEF meets the required quality. While it is true that the concentration is very important, there are many other important quality characteristics built into the ISO 22241 specification in regard to DEF.
Fleet managers responsible for procuring DEF should confirm that their suppliers are providing DEF that meets the ISO quality standard. One way to do this is to ensure that their supplier is providing a Certificate of Analysis (or Quality) with every shipment that addresses all of the quality characteristics that the specification requires.
Purchasing API-licensed DEF is the best way to be sure your DEF meets the rigorous requirements of the specification, because these products are not only tested before they are released to the marketplace, but they are also subject to testing in API’s Aftermarket Audit Program. Fleets and operators can always check to see if the DEF they are buying is licensed by visiting API’s real-time directory of licensees on the API website.
5. Managing DEF in Shops
For shops, the handling, storage and dispensing of DEF is very important so that off-spec DEF doesn’t reach the marketplace. Temperature during transport or at the point of storage or sale can harm the shelf life of DEF sold in containers.
Tips for Purchasing and Storing DEF to Preserve Quality
Make sure the stock is rotated to use the oldest product first. Proper storage temperatures in a shop is also vital. Storing in temperatures above 86° F will limit the shelf life of the DEF over time. Some additional things to consider in storing and handing DEF include the following:
- Bulk storage tanks should be dedicated for DEF. Don’t switch products in the bulk tank without thoroughly rinsing the tank with distilled or de-ionized water or on-spec DEF.
- A closed loop system for transferring DEF from a drum or bulk tank is recommended so contaminants don’t get into the DEF. This is particularly important in a shop or construction site that has dust or dirt in the air.
- Use dedicated equipment for dispensing DEF. Don’t use funnels, pitchers, hoses, etc. that are used for other fluids when putting DEF in a tank.
- Anything used for dispensing DEF should be cleaned with distilled or de-ionized water and followed by a DEF rinse. Don’t use tap water for cleaning.
For shops and operators, it’s important to know what you are putting into your DEF tank. The quality of the DEF going into your equipment is as important as the quality of the engine oils or fuels used in your equipment. Use of API-licensed diesel exhaust fluid will ensure that the DEF meets the high standards required by engine and vehicle manufacturers.
Jeffrey Harmening is manager-EOLCS/DEF/MOM for the American Petroleum Institute.
Troubleshooting 5 Common Decorative Concrete Sealer Problems
By JENNIFER CRISMAN at ForConstructionPros.com
Concrete sealer problems and the associated call-backs are one of the largest sources of frustration for decorative concrete contractors. When a concrete sealer does not look or perform as expected, the cause can usually be traced back to over-application, application in non-ideal conditions, or a build-up of multiple coats. Watch the video or visit the story on ForConstructionPros.com
Click here to watch the video on youtube
STIHL Chain Saw Safety, Operation and Maintenance Videos
Watch videos on chainsaw safety, operation and maintenance on your phone, tablet or computer. You can access these from the STIHL USA website or from Youtube. They will show you how to maintain your chainsaw, proper operation of the chainsaw and how to keep yourself and those around you safe while operating your saw.
STIHL USA website video archive click here
STIHL USA Youtube site click here
Search STIHL USA on your mobile phone Youtube app and you will find the chainsaw videos and videos for all types of STIHL equipment.
Tips for Tree Care and Storms: Before, During and After
As a third-generation arborist and three-time world tree-climbing champion, I've learned firsthand that trees are much more vulnerable than we assume. A tree might seem like it would be able to sustain the forces of a large storm, but sometimes internal damage is just too difficult to see. Ultimately, you want to be prepared before, during and after any storm – big or small.
Here are my Top Ten Tips for Weathering Storm Season:
Before the storm:
-
-
Conduct a pre-storm assessment. Identify trouble spots before a storm hits.
Some potential hazards to look for on your property:
- Cracks in tree trunks or major limbs
- Hollow, aged and decayed trees
- One-sided or significantly leaning trees
- Branches leaning more than 45 degrees over the roof
- Anything in close proximity to utility lines
- Shelf-like fungus or mushrooms
- Trees with dangerous leans
*Note: Several of these features may suggest that the tree may be suffering from a condition called heart rot or possibly buckling under its own weight, and causing danger.
-
Take measures to prevent damage.
After assessing possible hazards to your property, you and/or your arborist may need to take any number of measures to limit potential damage.
- Remove dead, diseased or damaged limbs
- Have leaning trees inspected and consider removing those with large cavities
- Prune branches too close to your house and over the street
- Check your gutters, and remove debris to prevent water damage. Many STIHL blowers can use optional gutter attachments.
- Call a professional to assess and potentially remove any within close proximity to utility lines; DO NOT attempt to do this yourself
During the storm:
-
Don't try to be a hero.
Your property is not more important than your life and the lives of your loved ones. Prepare in advance, follow guidelines for evacuations, and don't hesitate to get assistance.
After The Storm:
-
Put safety first.
It's important to protect yourself as well as your property.
- Be on the alert. Stay away from utility lines and keep an eye out for dangers both up in hanging branches and down on damaged trunks.
- Broken limbs may still be lodged in trees, but can easily and unexpectedly fall. Loggers call these "widow-makers."
- Look for trees leaning against or touching downed phone lines or power lines– a tree in contact with a power line, and the ground at the base of the tree, can be energized and dangerous.
- When in doubt, call your arborist (See #8 below)
- If you're skilled enough to do work yourself, suit up properly, wear the properattire and protective equipment. Many times we see newscasts of people wearing shorts and flip-flops to clean up storm damage. This is not what you should be wearing to do this type of work.
- Follow the guidelines in your instruction manual for any power equipment you're using.
-
Evaluate tree damage.
Evaluate your trees carefully by asking the following:
- Other than storm damage, is the tree basically healthy?
- Are major limbs and/or the leader branch still remaining?
- Is at least 50 percent of the tree's crown still intact?
- Are there remaining branches that can form a new branch structure?
If you answer "yes" to the majority of these questions, there is a good chance the tree can be saved. When in doubt, consult a professional.
-
Take Steps to Repair Minor Damage & Debris.
- Remove any broken branches or stubs still attached to the tree.
- Remove jagged remains of limbs to reduce the risk of decay agents entering the wound.
- Smaller branches should be pruned at the point where they join larger ones.
- Resist the urge to over-prune. Don't worry if the tree's appearance is not perfect.
-
Do not try to do it all yourself.
Evaluate what you can handle and what's for a pro – anything not on the ground should definitely be handled by a professional. Some of these things could be a threat to your life, so it makes sense to spend the money if you're not absolutely confident in your skills or if any of the below situations apply:
- Large limbs are broken or hanging or overhead chainsaw work is needed.
- If a tree is uprooted or downed, it can create an unnatural pattern of pressure points and tension. A chainsaw operator may be in severe danger if attempting to cut a tensioned limb or trunk (called a "springpole") – it may have an extremely violent, catapult-like reaction.
- If branches are too close or touching utility lines, report immediately to your local utility company. NEVER attempt to move downed utility lines.
- Any task you have not been properly trained to handle or are uncomfortable undertaking.
-
Consider wildlife.
Birds or bees may have been taking temporary storm shelter while you are doing work – always proceed with caution.
-
Stay educated.
Learn more tips on tree safety, chainsaw safety, finding a tree care professional, and how to prepare for storms at the following websites:
How do I pair a remote trailer mounted power module? Watch the manufacturer's video here.
Higher Ethanol Blends can Damage your STIHL Equipment
STIHL equipment was made to run on fuel containing no more than 10 percent ethanol. The same fuel you put in your car may not be the same fuel meant for your chain saw, trimmer, blower, or other STIHL landscape equipment.
What is the Difference Between E10, E15 and E85 Gasoline?
Today, there are more fuel choices for consumers than ever before.No longer can anyone go to a gas station and assume the fuel from the pump is safe and legal for all engines. Most fuel sold today at gas stations for automobiles and outdoor power equipment contains up to 10 percent ethanol (E10). However, in the past year, more gas stations are selling ethanol fuel blends greater than 10 percent – such as E15 and E85. STIHL outdoor power equipment is not made for ethanol blends higher than 10% ethanol or E10.
Don’t Pump the Wrong Fuel
In the past, consumers were physically kept from selecting the wrong fuel – with diesel you have to use a different pump, for example. This isn’t the case now as blender pumps, which dispense various ethanol fuel blends, become more widely available. The EPA has stated E15 and higher is not legal for use in off-road engine products, and only legal for a subset of automobiles. Yet, the only warning against “mis-fueling” is a small 3x5 pump label. Double-check the pump to make sure you put the right fuel in the right engine.
Why Are There So Many Different Fuels?
In an effort to meet federal renewable fuel standards, higher ethanol blends are being brought to market. When a small number of retail gas stations in select U.S. states began offering E15 and higher ethanol blends for sale in 2012, we at STIHL grew concerned. We want to protect our customers and future customers from inadvertently damaging their equipment by using the wrong fuel.
Most people believe any fuel sold at a gas station or other retail fuel station is likely legal and safe for any engine product. This is not true, and STIHL owners need to become aware of the fuel for which their equipment was designed, built and warranted – and use only that fuel.
To help keep your STIHL running strong
- Avoid E15 gasoline – too much ethanol can damage engine components
- Use a minimum of 89-octane gasoline.
- Use fresh fuel – Buy enough fuel to only last a two-month period (at most).
- STIHL recommends STIHL MotoMix® Patented Premixed Fuel a pure and stable fuel mixture that can be stored for up to two years in its original container.
Hard hat manufacturers recommend replacing hats every 4-5 years…even when they seem to be undamaged!
ANSI statute Z89.1-2009 requires particular information to be permanently printed inside each hard hat, including the date of manufacture. The longest a hat should be in service is four to five years from date of manufacture, according to the manufacturer’s guidelines. If the hat is not visibly damaged, you can calculate the expiration date by checking the date of manufacture. Additionally, workers should use a permanent marker to record the date they begin to use their head protection. This date will vary from the date of manufacture but may be needed for documentation in case of injury or accident. The manufacturer must also include the following information on the inside of the hat: manufacturer name, ANSI standard designation, and the appropriate ANSI class designation (Class A, B, or C).
An expiration date is a safeguard for a worker. Ideally a hard hat will be required to be replaced before it’s worn out in order to provide maximum protection at all times. If you work in the sun long hours or in extremely hostile environments with chemicals or high temperature, you may need to replace your hat after two years of use. Most manufacturers recommend replacement of the suspension inside the hat every 12 months. Proper maintenance of a hat ensures a longer life. Clean it with soapy water. Cleaning products may contain ingredients that could have an unfavorable reaction with a helmet, compromising its integrity before its expected expiration date. Don’t intentionally do anything that can shorten the lifespan of a hat, such as paint it. This essential piece of safety equipment must be kept in top condition.
The easiest test is to hold the hard hat with the suspension facing up and squeeze. If it feels brittle then replace it.
To check a hats manufacturing date, turn hat over and look for the in print of a circle with numbers around it. The arrow points toward the month and the 2 digit number on the inside of the circle is the year. Some manufacturers will print the date on the inside or even print a “use by date” on the inside of the hat.
SpecChem published the following document on Cold Weather Grouting and Repair
Cold temperatures delay set time and strength development of cementitious products and repair mortars. Cementitious grout and repair mortars, like concrete, must be allowed to attain a "green strength" before being subjected to freezing temperatures. The following guidelines may help compensate for cold temperature placement.
Click her to read the full article.
Take Your Office to the Construction Site with these Smartphone and Tablet Applications
By Keith Gribbins — Aug 02, 2013 Compact Equipment Magazine
Contractors are natural nomads. Each new job usually means exploring a new neck of the woods, always working in unique project parameters (from ground conditions and traffic control to equipment needs and zoning restrictions). For these rolling stones, the office has always been on site, in a truck or in the cab of piece of equipment. In the past, there might have been a disconnect between the bookwork and business of managing contract specifics and the actual administration and construction of a project on site. With the advent of laptops and cellphones, that information gap for on-the-road construction contractors, landscapers and farmers has shrunk considerably.
For high-tech equipment professionals today, something as small as a smartphone or tablet can take the mobile office to new dimensions of efficiency and portability. Everything from equipment maintenance to worker timesheets to government safety regulations can be managed using innovative and user-friendly software designed specifically for your mobile devices. These software solutions for smartphones and tablets are called “apps” (short for applications), and the professional equipment and contracting industries are full of them (half the time they’re free). On the next few pages, we’ve collected a few of our favorites. Feel free to download these apps yourselves, and see if they can really help streamline your mobile contracting operations.
Keith Gribbins is managing editor of Compact Equipment, based in Brecksville, Ohio.
We have listed below two of the apps that we thought would be useful to our customers.
NIOSH Ladder Safety
The National Institute for Occupational Safety and Health (NIOSH) announced the availability of a new Ladder Safety smartphone application. This new app uses visual and audio signals to make it easier for workers using extension ladders to check the angle the ladder is positioned at, as well as access useful tips for using extension ladders safely. The app is available for free download for both iPhone and Android devices. The app provides feedback to the user on positioning the extension ladder at the optimal angle. It also provides references and a safety guide for extension ladder selection, inspection, accessorizing and use. The app is based on a multimodal inclination indicator for ladder positioning that has been recently awarded a U.S. patent. For more info, visit www.cdc.gov/niosh/topics/falls.
OSHA’s Heat Safety Tool
When you’re working in the heat, safety comes first. With the OSHA Heat Safety Tool, you have vital safety information available whenever and wherever you need it — right on your mobile phone. This app allows workers and supervisors to calculate the heat index for their worksite, and, based on the heat index, displays a risk level to outdoor workers. Then, with a simple click, you can get reminders about the protective measures that should be taken at that risk level to protect workers from heat-related illness, as well as reminders about drinking enough fluids, scheduling rest breaks, planning for and knowing what to do in an emergency, adjusting work operations, gradually building up the workload for new workers, training on heat illness signs and symptoms and monitoring each other for signs and symptoms of heat-related illness. For more info, visitwww.osha.gov/SLTC/heatillness/heat_index/heat_app.html.
The information above is from the current edition of Compact Equipment Magazine.
The Compact Equipment Magazine had the following article on Take Care of Your Tires posted on their website
Proper Tire Maintenance Will Keep Your Fleet Operating at Maximum Efficiency
Michael Ford — Jul 01, 2005
Tires are an afterthought to many contractors and operators. They take them for granted, don’t maintain them properly and yell and scream when a flat tire causes one of their machines to go down and lose productivity. Many times, however, these problems are completely avoidable through proper tire maintenance.
Contractors who take care of their tires can see the results in increased profits because their machines aren’t offline. A more comfortable ride equates to a more productive employee, not to mention that maintained tires are safer.
There are several things an operator can do to maximize the tire’s life. The most important steps are to select the best tire for the application, run the manufacturer’s recommended air pressures and follow a recommended tire maintenance schedule. Making sure your machine operators are properly trained and that hazards around the worksite are minimized are two other, often overlooked steps that will make a big difference in maximizing the life of your tires. A daily, weekly, quarterly and annual maintenance routine for skid steer tires is a must.
Small construction tires can be relatively simple to maintain if the operator follows the basic rules. Check tire pressures weekly and always at the start of a work shift to ensure the pressure readings are correct, always have valve caps in place and ensure that tire rims are in proper working condition.
The estimated industry average for skid steer tread life is between 400 and 600 hours, depending on the application, operator skill and tire maintenance schedule. Abrasive surfaces, such as concrete and asphalt, and work areas with severe hazards, such as waste transfer, demolition and metal recycling, will result in faster worn tires.
That’s why it’s important to choose the correct tire for your skid steer.
The main options center around traction vs. protection. Entry-level priced tires are traction oriented with little protection in the sidewall or tread. As price increases, so does the amount of sidewall and tread face protection while maintaining traction.
The way your skid steer is running can tell you a lot about your tires. If the tires are over-inflated, the machine will bounce like a basketball and be difficult to control. If the tires are under-inflated, the machine will feel unstable when the loader arms are lifted to full height.
So what can operators do to ensure that they are getting the most out of their tires? The answer is simple: Evaluate tire wear on a routine basis.
There are two areas to look at when evaluating tire wear — the tread and the sidewall. Look for signs of cutting, chunking, punctures and rubber tearing. This will help you to determine if the tire is properly inflated and/or matched to the application. Also, measure the tread depth on a weekly or monthly basis by using a ruler or tread depth gauge to determine the average wear rate. Compare this wear rate to other tires and machines.
And always remember that if you work on your own tires, the most critical element is to ensure the tire is fully deflated before working on the tire. After removing the valve cap and valve core to deflate the tire, continue to ensure the valve is free of obstructions so that the air inside can fully deflate.
But what about those who still don’t take tire maintenance seriously?
If proper tire maintenance is not a priority, an operator is virtually guaranteeing he will reduce the tire’s tread life, increase the likelihood of tire-related failures (punctures, running flat, etc.), reduce the machine’s productivity and unnecessarily cost the company money. Not only do you have to pay to repair or replace the tire, but you lose the productivity of that machine, which also costs your company money.”
10 Tire Maintenance Tips:
There is no time like the present to start following important maintenance tips to ensure your tires operate at peak levels throughout any season. The key is checking tires regularly. Routine maintenance reduces downtime, eliminates preventable major repairs, improves operating efficiency and promotes higher levels of productivity. Simply translated, 10 simple steps can save you considerable time and money.
Step 1
Conduct a visual inspection of your vehicle’s tires prior to operation. Look for signs of irregular wear in the tread or shoulder of the tire and examine the tire for bubbles
or bumps caused by air infiltration or foreign objects. If you notice either of these symptoms, have the tire repaired promptly because both can lead to tire failure and potential danger.
Step 2
If you notice deep cracks, cuts or other major problems during the inspection, don’t operate the vehicle. Have a trained service person diagnose the severity of the problem and make the proper repairs. Never allow an unskilled person to attempt repairs because incorrectly mended tires can lead to performance problems in the future or even result in personal injury if the tire fails.
Step 3
Check tires for correct air pressures. Perform this step daily on vehicles in constant use because air pressure is critical to a tire’s performance. Check air pressure weekly on vehicles with less demanding schedules.
Step 4
Check the vehicle’s owner’s manual to determine precise air pressure. It should provide initial data on the weight of the vehicle and standard load. Your tire distributor can help pinpoint the exact air pressure recommendations for your tires based on the manufacturer’s requirements and the application in which the vehicle is being used.
Step 5
Never operate a vehicle that has flat tires, damaged or distorted rims or wheels, missing bolts or cracked studs. Any of these symptoms could be dangerous.
Step 6
Never weld or apply heat to parts of the wheel near the tire. Heat causes serious damage to tires and can cause them to explode. Tires always should be removed before these types of procedures are conducted.
Step 7
Store tires properly when they are not in use. Place them in a cool, dry place away from direct sunlight to avoid premature aging. Also, prevent exposure to ozone sources such as sun, arc-welders and mercury vapor light bulbs, as well as ultraviolet rays and inclement weather. Store tires standing upright on the tread and avoid stacking, which can weaken the tires on the bottom of the stack.
Step 8
Avoid lifting tires through the center with a crane hook, because this can damage the critical bead area. Instead, lift the tire under the tread by using flat straps. Flat straps are recommended over steel slings or chains because they will not cause cuts or abrasions.
Step 9
Deflate the inner and outer tires of a twin fitment before removing any rim fixture from the hub of the vehicle.
Step 10
Avoid mixing tires on your vehicle — for example, pairing a normal tread depth with a deep tread depth or a bias-ply tire with a radial. Using two different types of tires could cause damage to the vehicle’s internal components because the tires do not work together to provide the same traction and handling performance.
Proper tire maintenance impacts the entire jobsite by keeping fleets operating at maximum efficiency. By following these 10 simple steps, your operation can take advantage of its tire investment and boost productivity levels.
Michael Ford is the market segment manager at Michelin Earthmover, Greenville, S.C.
The September 2012 Compact Equipment Magazine had the following article on selecting a portable air compressor
Consider Multiple Factors when Selecting a Hand-Portable Air Compressor
By Dan Leisse — Sep 04, 2012
Selecting an air compressor at first seems so simple. How tough could it be? All you have to figure out is how much air you need and decide how much you want to spend. Right? Actually, there are multiple factors that must be considered to find the right compressor for the job. From air pressure to horsepower, a contractor must identify the proper balance of features to meet his or her needs. Let’s break out some of the key factors to help make the decision process a little easier.
Portability, Flexibility Needs
When looking at hand-carry or wheeled air compressors, portability will be a given. The bigger concern will be ensuring the model also meets the pressure and capacity requirements of the job. With their low weight and compact configuration, these air compressors can go pretty much anywhere — with one condition — which is what we need to look at next.
Power Source
The next obvious step involves considering where the compressor will be used. If working in a remote area without access to electrical power, either from the grid or from a generator onsite, the only choice is a gasoline engine model. That will offer mobility around any jobsite. But there may be other issues that come into play, such as environmental restrictions — emissions in a confined space or noise abatement — that cancel out the advantage of convenience. The gasoline model also will have both a higher purchase price and the ongoing costs will be greater, but it will provide higher actual horsepower than its electric-motor counterpart.
CFM Required
Besides power, capacity will directly impact what the compressor can do. Begin by adding the CFM (cubic feet per minute) requirements for all the tools that will be used simultaneously, and then add another 30 percent to allow for unknown or uncommon compressor usage. The CFM rating can be found either on the tool itself or in the owner’s manual. It can be figured three ways:
1. Displaced CFM (DCFM) is simply a mathematical calculation of the bore, stroke and rpm. But, it does not take into account any of the important variables, like temperature, atmospheric pressure, humidity, friction or heat dissipation, and therefore it means almost nothing in the real world.
2. Standard CFM (SCFM) is a better measure of reality. SCFM is the flow of free air in a standardized environment — such as 14.5 psi atmospheric pressure (the pressure at sea level), 68 degrees Fahrenheit and 0 percent humidity.
But what about individual needs? For example, if someone is working in mile-high Denver in January, it surely isn’t going to be 68 degrees. Or, a person could be in Louisiana in July, and the humidity is off the charts.
3. Actual CFM (ACFM) figures in the variables that apply to unique situations. It will provide output of the pump for the actual working conditions. But ACFM is a hard figure to get, precisely because it does require site-specific data and calculations that may be best left to an engineer.
For selection purposes, the best bet is to compare compressors based on the SCFM ratings. This puts all units on a level playing field for a true apples-to-apples comparison.
Required Operating Pressure
CFM will also be important to know when considering a single-stage compressor vs. a two-stage model. Begin by listing the minimum operating pressure requirements for the tools that will be used, which will indicate whether a single- or two-stage compressor is needed. Single-stage compressors are fine up to 150 psi. Anything more will require a two-stage. A single-stage compressor will typically have a higher CFM rating, because the cylinder is drawing in air and compressing it with every rotation, whereas a two-stage is compressing the air up to an intermediate pressure in one or more cylinders and then passing it on to another cylinder to finish the job. Because the air is typically passed through an intercooler between stages, a two-stage compressor is more efficient at higher pressures.
Receiver Tank
Once again, the capacity of the compressor tank, which is usually measured in gallons, depends on how the compressor will be used. If running tools that require quick, concentrated bursts, such as nail guns, a small tank is best. If the tools are to be used for sustained periods, such as impact wrenches, a larger tank will work better.
Overall, the most critical issue to keep in mind is job analysis. To select the right compressor for your operation, it’s best to understand the requirements of your current and future projects. Start by creating a realistic checklist using the factors outlined above. From there, it will be much easier to find a unit that will meet your needs and keep your business powered for years to come.
Dan Leiss is president of Jenny Products Inc., based in Somerset, Pa.
Before Compressor Operation Begins
Make sure the air compressor is clean from previous work. It will be easier to detect leaks and broken or loose components on a clean machine. Before turning on the machine, do a visual inspection. Check the hoses for kinks and the electrical wiring, tubing and piping for any damage. Also check the controls, gauges, accessories and instruments to make sure there are no loose mountings or visible damage. Check all connections and tighten any loose nuts and bolts.
The next step is to check the pump oil level. To do so, first disconnect the power source and place the compressor on a flat surface. Remove the oil fill plug and check the level, then insert a screwdriver into the crankcase. Inspect the oil on the screwdriver. If there are signs of contaminants, such as water or dirt, change the oil. Otherwise, change the oil annually. If a gas engine powers the compressor, check the engine oil level, as well, which also should be changed annually. Fuel filters may be changed to accommodate an air compressor’s daily task. There are two types of filters: standard and coalescing. A standard filter will trap dust particles based upon micron size, while a coalescing filter will remove water and oil from the air. Provided the correct filter is used for each application, it should only need to be replaced monthly or every few months.
Click here for Portable Air Compressors
Click here for Towable Air Compressors
The June 2012 Compact Equipment Magazine had the following article on track loader maintenance
Maintenance Tips for Keeping Your Compact Track Loader Running Reliably
Compiled by CE Staff — June 21, 2012
A compact track loader is one of the most versatile and useful tools within a contractor’s equipment fleet, providing improved capability over soft terrain and increased capacity compared to skid steer loaders. However, the very items that make them unique and so useful also require some special care to ensure reliable service and uptime.
Maintaining the operators area is not that much different than on other pieces of equipment except that when track loaders are operated on hard surfaces, vibration of the cab and components is more intense. New track loader designs have taken steps to provide a smoother ride. Over time, intense vibration can lead to more maintenance depending on specific applications and operating conditions (like operation in soft soils vs. operation with a cold planner on concrete). With this in mind, an operator should pay special attention to hardware to ensure that all components stay securely in place. Cab mounts, seals and hardware should be checked on a regular basis. Loose components and hardware should be tightened, and damaged components should be replaced.
Track loaders are generally operated in dirty or soft ground conditions. Operators entering the cab tend to bring in a lot of soil and mud on their boots. As with most other products, the operator’s area needs to be cleaned on a regular basis. If the floor pod does not tip forward for easy clean-out, a shop vacuum should be used to ensure debris is removed. This is particularly important if the unit is equipped with an enclosed cab and air conditioning or heat. If the cab is equipped with a re-circulating air filter and a cab fresh air filter, they should be serviced on a regular basis. Keeping the air conditioner clean will ensure its long-term reliability.
The operator’s manual supplied with the product provides critical safety information and instructions on normal engine and hydraulic system oil and filter change intervals. Track loaders operate in fairly difficult conditions; spending a few extra dollars for regular oil sample testing will maximize your change intervals and help to ensure you are changing your oil and filters adequately. Oil sampling will also provide short- and long-term indicators of unusual wear or failures that are in progress to help eliminate downtime during critical periods.
Since track loaders are uniquely qualified to operate in harsh soil conditions, it is also important to check the chassis. Be sure all covers, doors, belly pans and shields are in place, in good condition and securely fastened. Manufacturers recommend the chassis be kept clear of debris, and in most cases, cleaned daily. This is required to prevent catastrophic failures due to accumulation of foreign material or overheating due to plugged radiators. The heart and soul of a compact track loader is its undercarriage and track system. Proper operation and maintenance will either lead to greater productivity or downtime and high operating expense. Proper operation and maintenance is not difficult, but does require following recommendations in your operator’s manual.
Track tension is very important to extend the life of tracks and the rolling elements of the undercarriage. In fact, improper track maintenance may be the single largest contributor of premature wear and failure of tracks and components, especially if tracks are over-tightened to delay normal adjustments. Over-tightening the tracks also robs horsepower and increases the likelihood of damage to tracks during machine operation. Don’t forget to inspect the track on a regular basis.
Overall, track loaders offer many operating advantages over wheeled loaders depending on soil conditions and allowing improved productivity. In fact, track loaders remain productive when select soil conditions make wheeled machines useless. But as with any machine, they must be maintained properly. A little extra time spent on them each day before they are operated will increase their productivity and ensure they are operating when they should be.
A recent article from September 2011 Compact Equipment Magazine had the following article on using a Hole Digger
Smart Tips for Simple Hand-Held Earth Auger Operations
Dennis Von Ruden — Sep 07, 2011
Jobsites don’t see too many machines simpler than an earth auger. However, manufacturers build them this way because there’s just no reason to make them complex. Even an auger’s purpose is simple. Whether the application is construction, landscaping, fence installation or a homeowner project, earth augers do one thing and one thing only — dig holes.
But while the equipment and its function are not complicated, not everyone will achieve the same level of success with a hole digger. There are some basic operational hints — along with a list of mistakes to avoid — that should be considered in order to ensure safety and maximize productivity on the job.
Ready to Dig?
There’s no sense in getting started until both the equipment and operator are prepared to go to work. Assuming the hole digger itself has been properly maintained and is in good mechanical condition, the first thing the operator should do is examine the auger’s common wear parts, such as the screw bit and teeth.
The screw bit is the very tip of the auger. If it is extremely worn — or perhaps even completely gone — the auger will not track straight as it digs. Augers can dig aggressively when their teeth are in good shape, but if not, the auger flighting must pick up the slack and absorb unnecessary wear. Worn teeth can also decrease digging capacity and force the auger to become stuck in the ground.
Next, take time to read over the operator’s manual. While this task may seem unnecessary to some experienced operators, it’s still an important step — particularly if it’s been a while since the operator has used a hole digger, or if the equipment works a little differently than augers he or she has used in the past. Manufacturers cover just about everything there is to know about safe and efficient operation in their manuals. This information is invaluable for novices, and giving the manual a quick read might even teach an old dog a few new tricks.
After reading the manual, the next step is to identify underground obstructions. Always call an underground locating service before you dig to identify the whereabouts of buried lines. Also, beware of natural obstructions like rocks or tree roots. Grass and other overgrowth can also hamper an auger’s digging ability by clogging the auger blade and screw bit, and therefore should be removed to increase efficiency and overall productivity.
Proper Start-Up
Once all the jobsite parameters have been established, it’s time to get digging. Pay attention to the operating instructions for starting the hole digger’s engine. The machine is designed to keep the operator away from the engine exhaust muffler. With an improper operating position, the operator runs the risk of serious injury from coming into contact with the hot surface of the muffler or from inhaling high levels of carbon monoxide.
Allow the engine to properly warm up to the point where it will operate without the engine choke. Keep in mind that in cold weather, initial starting may require more pulls. Once running, if the hole digger or an individual component or accessory does not appear to be functioning properly, stop immediately and correct the problem before resuming work.
Normal operating procedure for a handheld hole digger is to dig with the engine going at full speed. This allows the unit’s centrifugal clutch to become more firmly engaged, thus transmitting more usable power to the auger. When using a hole digging attachment, proper auger rpm will vary, but generally the operator should feed the auger as fast as soil conditions will allow.
Kickback, Don’t Relax Position
When working in areas with rocks or other obstructions that could be struck by a handheld auger, an operator should be prepared for the occurrence of kickback force. If kickback is anticipated, the hole digger should be operated at less than full speed to ensure a more rapid release of the centrifugal clutch when an obstruction is encountered.
An operator can minimize the effects of kickback through proper body positioning. Keep the left side of the equipment handle as close as possible to your left hip and leg area. Your upper arms should be kept close to the body to maximize mechanical leverage. Keep your back vertical by bending your legs as needed while digging, and position the left foot ahead of the right foot at a comfortable distance.
Experienced operators who understand kickback sometimes choose to absorb its effects while attempting to use the auger blade to “chip” their way around or through an obstruction. This technique usually involves holding up on the operator handle and establishing a minimum feed rate for the auger. Often the nature and size of a buried object will simply prevent the auger from passing by or going through it, forcing workers to find a more suitable tool to remove it. The main point is that kickback is manageable when proper operating position is maintained, but is equally challenging if the operator is not prepared for it.
Operators would be well advised to wear gloves while running a hole digger and should always keep a firm and steady grip on the handles. This helps to reduce fatigue, as well as increase productivity. If an operator ever realizes that he is in the process of losing full control of the hole digger for any reason, he should push himself free and clear from the handles.
In the Hole
As a general rule, pressing down on the operator handles is not required to initiate or sustain the digging process. In lower density (soft digging) soils, it may be necessary to hold up on the handle to reduce the digging rate of the auger. In higher density (hard digging) soils, an operator might need to press down on the handles to establish acceptable digging rates. Operators should make judgments based on their individual levels of experience to prevent the auger from burying itself in the hole, which is typically the outcome when allowing the auger to feed at an excessive rate.
Occasionally, operators will wind up stopping the engine while the auger rests in a partially or completely dug hole. Only a skilled operator should attempt to restart the engine while the auger remains in the hole. The more accepted procedure is to first remove the unit from the hole, and then return it to the hole with the engine running only at idle speed. One exception for this is during the use of auger extensions.
Extensions are often called upon when standard length augers are insufficient. Using extensions is a vastly superior alternative to feeble attempts of some to force a standard auger to drill down to extreme depths. This error in judgment usually ends with an auger buried in the ground. The mistake is commonly multiplied when operators try to back the auger out with pipe wrenches. When this exercise proves unsuccessful, some try yanking the auger out with a backhoe or skid steer, which almost always results in the auger becoming bent and broken.
Dig No Further
Of course, no amount of operational advice can really substitute for actual experience. Hole digging professionals develop a natural feel for their craft over time. But new equipment innovations are constantly hitting the market, which means it’s always a good idea to peruse the manual or call the manufacturer for operating tips from time to time. With the right combination of experience, common sense and occasional re-education, auger operators can continue to hone their hole-digging skills to get the most out of their equipment on the job.
Dennis Von Ruden is the president of General Equipment Co., based in Owatonna, Minn.
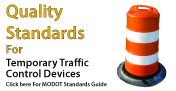
Temporary traffic control devices are a necessary part of highway work zones. These devices are used to warn motorists of hazards, advise them of the proper path through the work area, delineate areas where they may not operate, and to separate them from workers and opposing traffic.
There are many factors that ensure the success of these functions; the performance and condition of each temporary
traffic control device are two such factors. Whenever worn or damaged devices appear in a work zone, the general quality of the work zone deteriorates. This situation may reduce the level of safety provided to the workers, pedestrians, and traveling public due to the road users’ loss of confidence in and compliance with the devices.
It is with this possibility in mind and to provide the means for complying with MUTCD Sec. 1A-05., Mo-DOT established the Quality Standards for Temporary Traffic Control Devices handbook. The quality standards contained herein are applicable to all temporary traffic control devices (e.g., impact attenuators, truck mounted attenuators, signs, channelizers, barricades, warning lights, changeable message signs, flashing arrow panels, work zone traffic signals, lighting units, temporary pavement marking, temporary traffic barrier, etc.) deployed on the state highway system. The end result of its effective application is a benefit to the well being of those who work in or navigate through work zones located on state highway right of way.
Click here for the Guide
Dayton Superior Paving Products Guide
Click the link below for the Dayton Superior Paving Products Guide. If will help you in estimating what you need on a jobsite. Remember to always consult with your paving products supplier when doing job estimates. Contact one of our sales team or estimators for assistance when bidding on your next job.
Dayton Superior Paving Products Guide
How to keep your generators and compressors running cool!
When operating a piece of equipment in a cabinet (tow behind compressors and generators). Keep the doors closed. This will allow the cooling system to operate as designed and keep noise emissions down. Also remember to check all fluids and keep the radiator clean (if applicable).
SpecChem Product Calculator
Click here for calculator
Product Selector
Product Crossover Reference
You can also find a link to the SpecChem product selection wizard and other useful product information when you click the link for the product calculator.
How to choose a pressure washer
Choosing The Right Pressure Washer
Choosing the right pressure washer for the job is as important as how you use it. The right pressure washer will clean faster and more effectively. Key factors in making your choice:
- Hot or cold: Hot water pressure washers clean faster and better. If you’re cleaning floors or engines with grease or oils, hot water is a must. You wouldn’t think of washing greasy plates in the kitchen sink with cold water. The same applies to power washing. If you operate cold water equipment more than a few hours a week, you should closely consider the labor savings you could realize by switching to a hot-water pressure washer.
- Belt or direct: If you’re going to be operating pressure washer as much as five or more hours per day, five days a week, then consider a belt-drive model in which a vibration-absorbing belt connects the pump to the motor or engine. On the other hand, direct-drive models, where the pump is coupled directly to the motor or engine, are more compact and economical.
- Gas or electric: Traditionally electric-powered pressure washers are less expensive, but are “tethered” to an electrical outlet. Pressure washers with gasoline-powered engines are much more portable, but they’re limited to outdoor use.
In addition to these basic decisions, users should look for equipment that is easy-to-use, safety certified, and efficient to operate.
|
|